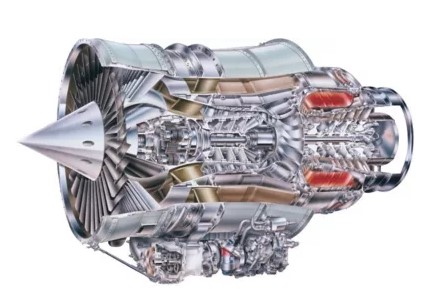
Retos y soluciones en el diseño de turbinas
Ya sea para el desarrollo de motores o la maduración de la tecnología, el enfoque de los fabricantes de turbinas de gas varía de un módulo a otro, pero finalmente se une a cuatro áreas tecnológicas en competencia:
- + Cumplir con los requisitos normativos sobre emisiones, ruido y seguridad
- + Construye un motor eficiente
- + Excede los requisitos de durabilidad
- + Supere las limitaciones de peso o de consumo específico de combustible
En las últimas décadas, se ha hecho posible mejorar la eficiencia del motor en el ciclo Brayton centrándose en algunas palancas, como aumentar la relación de presión general, aumentar la temperatura de entrada de la turbina, usar materiales avanzados y reducir el tamaño del motor central. Estas mejoras han resultado en la aparición de aeromotores compactos con interacciones estrechas y complejas entre todos los módulos.
Estos logros tecnológicos se lograron perfeccionando el rendimiento de cada módulo (ventilador, compresor, cámara de combustión y turbina) y cómo se unen para formar una máquina notable. El diseño por análisis y la validación por prueba han hecho que este viaje sea posible y más rápido.
Debido a que los grupos de diseño en los OEM están aislados, simular cada módulo de la turbina de gas por separado sigue siendo una práctica común. Modelar la interacción entre estos módulos sigue siendo complejo. De hecho, la naturaleza compacta del núcleo del motor dificulta la identificación de una ubicación de interfaz clara entre los componentes. En la sección caliente, la cámara de combustión y la turbina de alta presión (HPT) generalmente se modelan por separado con las condiciones de contorno transferidas a la entrada de la turbina. Este enfoque no es ideal para capturar todos los intrincados detalles del flujo que viajan entre la cámara de combustión y la turbina y para rastrear la migración de la racha caliente que determina la durabilidad de la turbina. El modelado de la interacción entre el combustor y la turbina requiere una metodología práctica que se pueda aprovechar durante el proceso de diseño del motor al tiempo que garantiza soluciones CFD precisas, rápidas y sólidas.
Modelado de componentes estáticos en la interacción turbina-combustador
El primer paso para modelar la interacción combustor-turbina es comenzar con los componentes estáticos. Se consideraron dos enfoques de modelado para las simulaciones que se muestran en este blog. El primer método, la cosimulación, resuelve los dos componentes de forma independiente y transfiere perfiles 2D desde la salida de la cámara de combustión hasta la entrada del estator. A diferencia de los métodos tradicionales de transferencia unidireccional, se utilizó un método de acoplamiento bidireccional que resultó en un bucle de retroalimentación de intercambios de perfiles hasta que se alcanzó la convergencia de cada componente. El segundo método, la simulación conjunta, resuelve la cámara de combustión y el estator en el mismo dominio computacional.
El enfoque de co-simulación viene con el desafío de encontrar ubicaciones de interfaz adecuadas que definan la salida de la cámara de combustión y la entrada de paletas. La naturaleza compacta del motor combinada con la presencia de canales de enfriamiento y salidas de purga dificulta la definición de la región de superposición entre el dominio de la cámara de combustión y el dominio de la paleta del estator. El enfoque de cosimulación también se adhiere a las prácticas de modelado actuales en las que la cámara de combustión se resuelve con simulaciones de resolución de escala, como la simulación de remolinos grandes (LES) o la simulación de remolinos mezclados por tensión (SBES), mientras que la turbina se modela con Navier-promedio de Reynolds. Stokes (RANS). Las cantidades promediadas estadísticamente, como la presión total, la temperatura total y los componentes de velocidad, se interpolan dentro de la cámara de combustión y se aplican a la entrada de la paleta del estator como condiciones límite. Se presta especial atención a la extracción precisa de las cantidades de turbulencia, como la intensidad de la turbulencia y la escala de longitud de las carreras de LES de la cámara de combustión, porque se sabe que estos parámetros tienen un gran impacto en la mezcla y la transferencia de calor en la turbina.
El enfoque de simulación conjunta es más sencillo con un solo dominio computacional donde la simulación de resolución de escala y el flujo de reacción prevalecen en todo el modelo. La malla se refina para hacer una transición suave de los requisitos de la cámara de combustión a las paletas, especialmente cerca de las paredes.
El enfoque de cosimulación requiere al menos un bucle de retroalimentación para alcanzar la convergencia en el doblete de combustor y paletas. Lo que significa que los perfiles de condiciones límite y los parámetros de rendimiento en ambos componentes (perfil de salida de temperatura de la cámara de combustión, caída de presión total, presión de entrada de la turbina) se estabilizan dentro de un umbral dado después de dos simulaciones de la cámara de combustión y dos ejecuciones de paletas del estator. En contraste, la simulación conjunta requiere solo una sola ejecución, por lo que tiene la ventaja de requerir un 50% menos de tiempo que la co-simulación.
Un aspecto importante de la comparación de simulación conjunta y cosimulación es comprender el impacto de cada método en la distribución de temperatura y la carga térmica de la pared del álabe. La distribución de temperatura promediada circunferencialmente aguas arriba del borde delantero de la paleta muestra poca diferencia entre los dos métodos. Sin embargo, aguas abajo del borde de fuga, las variaciones son más pronunciadas, especialmente en el buje y el obenque. Los contornos de temperatura cerca de la pared en el doblete de paletas son similares en las simulaciones conjuntas y conjuntas, mientras que ambos exhiben diferentes gradientes radiales en cada paleta del doblete.
Cuando el acoplamiento se limita a los componentes estáticos, la simulación conjunta es más práctica en cuanto al proceso y más eficiente en cuanto al tiempo de cálculo, al tiempo que proporciona una precisión similar a la de la cosimulación en la predicción de la interacción entre el combustor y el estator.
Las simulaciones de rotor plantean preguntas
A medida que incluimos el rotor en las simulaciones conjuntas y conjuntas, las condiciones de modelado cambian. La cosimulación aún requiere al menos un circuito de retroalimentación entre el modelo de cámara de combustión y el modelo de estator-rotor. Sin embargo, la escala de tiempo de simulación conjunta cambia para ajustar la frecuencia de paso de las palas del rotor con un paso de tiempo que es un orden de magnitud más pequeño que el paso de tiempo de la cámara de combustión. La simulación conjunta ahora requiere un tiempo de respuesta significativamente mayor para completar la simulación de resolución de escala desde la entrada de la cámara de combustión hasta la salida de la turbina.
La pregunta es: ¿Los beneficios de ejecutar una simulación conjunta en términos de interacción bidireccional de la turbina del combustor superan el tiempo que lleva obtener una solución? Este será el tema de nuestro siguiente artículo.