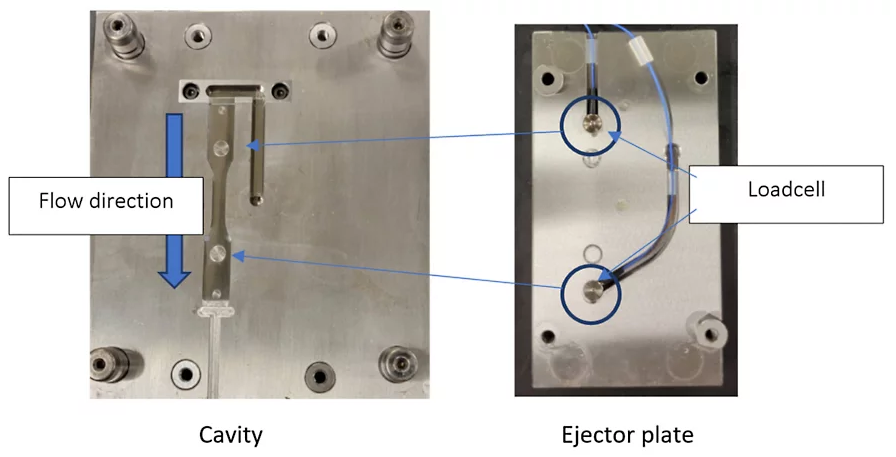
Las startups emplean la tecnología de gemelo digital para validar el moldeo por inyección
El moldeo por inyección es quizás la forma de fabricación más común en todo el mundo debido a su capacidad para escalar la producción en masa. Esencialmente, el proceso consiste en inyectar plástico licuado calentado en moldes de temperatura controlada a alta presión y luego enfriarlos. Estos materiales de polímeros plásticos también se conocen como termoplásticos y son flexibles al calentarse pero solidifican cuando se enfrían.
Desde tapas de botellas y juguetes hasta piezas electrónicas y automotrices, el moldeo por inyección es un componente central de la producción en masa. Sin embargo, si bien su capacidad de repetición y consistencia es atractiva, un desafío importante es evitar errores de diseño. Un error de diseño pasado por alto producido por millones puede descarrilar significativamente los plazos y presupuestos de producción.
MAZIN Inc., una startup de Internet industrial de las cosas (IIoT) con sede en Japón, está desarrollando una forma de prevenir este posible error masivo mediante el uso de sensores como otro par de ojos a través de las soluciones de simulación y la tecnología de gemelos digitales de Ansys.
Mazin utiliza máquinas de moldeo por inyección, equipadas con sensores, para recopilar datos de fluctuación de presión que se utilizarán dentro de sus gemelos digitales.
Detección por Inteligencia Artificial
Fundada en 2018, MAZIN investiga y desarrolla algoritmos de inteligencia artificial (IA) para plataformas IIoT para ayudar a las fábricas a convertirse en fábricas «inteligentes» mediante la implementación de tecnologías de IA para ayudar a la producción.
Recientemente, al integrar Ansys Twin Builder y PlanetsX, un producto complementario de Ansys proporcionado por Cybernet, el socio de canal Elite de Ansys, los ingenieros de MAZIN han desarrollado un sistema basado en IA para monitorear el ajuste de la condición durante el proceso de moldeo por inyección.
Uno de los principales desafíos en el moldeo por inyección es controlar el flujo de resina en los moldes. Con la ayuda de la simulación, MAZIN está implementando sensores virtuales para monitorear este flujo y mejorar la precisión.
“Nuestros clientes de moldeo por inyección tienen problemas para predecir el flujo de resina en las cavidades del molde y ajustar las condiciones de la máquina para mantener la calidad del producto”, dice Yusuke Uchiyama, director de investigación de MAZIN Inc. en Japón. “Para resolver estos problemas y mejorar la capacidad de predecir las características del flujo, decidimos emplear la simulación Ansys, que es útil y beneficiosa tanto para los ingenieros de diseño como para los de procesos”.
Mazin mide los datos de presión de la cavidad con celdas de carga en pines eyectores (como se muestra arriba) y combina estos datos medidos con la simulación de flujo de resina de PlanetsX para crear un ROM (modelo de orden reducido) con Ansys ROM Builder.
Por ejemplo, Uchiyama y su equipo midieron la presión de la cavidad mediante la instalación de sensores de presión de celdas de carga en la parte posterior de los pasadores eyectores en los lados aguas arriba y aguas abajo de cada cavidad del molde de una máquina de moldeo por inyección.
A continuación, el grupo simuló el flujo de resina en PlanetsX para medir la fluctuación de presión provocada por la fuerza de la resina que empuja contra los pines eyectores.
Izquierda: imagen real de la máquina de moldeo por inyección. Derecha: relación posicional del sensor, la cavidad y el pasador.
PlanetsX es una herramienta disponible a través de la plataforma de integración de simulación Ansys Workbench que proporciona un análisis consistente del moldeo por inyección y admite la simulación de deformación mediante el uso del historial de flujo de simulaciones lineales y estructurales. La deformación, o alabeo, es un defecto que ocurre cuando la forma deseada de una pieza moldeada se distorsiona durante el enfriamiento.
Después de combinar los datos de presión recopilados de los pines eyectores con el resultado de la simulación PlanetsX, el equipo construye modelos de orden reducido (ROM) utilizando el generador de ROM de Ansys y Twin Builder. Con esta información, Uchiyama y su equipo desarrollaron un clasificador de árboles de decisión para la calidad de producción del moldeo por inyección. En la IA y el aprendizaje automático (ML), los árboles de decisión organizan el proceso de toma de decisiones paso a paso para configurar algoritmos para la IA que extraerán la información necesaria de los datos proporcionados en cada paso.
El algoritmo utiliza los resultados de su simulación y las ROM, aplicando datos estimados como salida y datos experimentales como entrada. Para lograr esto mejor, el algoritmo usa los datos del sensor de presión de un punto de observación para estimar la presión en un punto de evaluación en la ROM. Como resultado de este método, puede ampliar la cantidad de información en función de una cantidad muy pequeña de datos del sensor.
Izquierda: Posiciones de medición de sensores reales y virtuales. Derecha: forma de onda de presión en serie temporal que muestra datos reales del sensor (lado superior) y datos del sensor virtual (lado inferior).
Rompiendo el Molde: Resultados Ganadores
Uchiyama dice que el generador de ROM fue particularmente beneficioso.
Twin Builder utiliza ROM producidos a partir de productos estructurales, de fluidos, electromagnéticos y semiconductores de Ansys para modelar ensamblajes mecánicos, integridad térmica y más.
En este proyecto, MAZIN construyó ROM aplicando redes neuronales, que son modelos deterministas con entradas conocidas. En etapas futuras del proyecto, el equipo planea desarrollar modelos estocásticos reducidos con entradas y variables desconocidas.
Las ROM se pueden crear en Workbench e importar a Twin Builder. La cosimulación con solucionadores de física 3D conserva la precisión total del análisis de elementos finitos (FEA) y la dinámica de fluidos computacional (CFD) para modelar componentes de fluidos, redes de flujo, ensamblajes mecánicos y más.
Además del reciente proyecto de moldeo por inyección, MAZIN ha desarrollado sistemas de IA de detección de anomalías para centros de torneado y mecanizado.
“Comenzamos a utilizar Ansys Twin Builder para mejorar la productividad de nuestros clientes en los procesos de fabricación, por ejemplo, en casos de procesamiento de torneado y mecanizado, moldeo por inyección, fundición a presión, etc., para poder brindar información física a nuestros clientes durante sus procesos de fabricación”, dice Uchiyama. «El uso de la tecnología ROM a través de Ansys Workbench redujo nuestro tiempo de simulación general en aproximadamente un 50-70 %».
Para el proyecto de moldeo por inyección, los ingenieros de MAZIN realizaron pruebas de aprobación o falla para determinar los defectos o fallas del moldeado, también conocidos como intentos cortos, y el éxito de la predicción del sensor. En el moldeo por inyección, se producen disparos cortos cuando la cavidad del molde se enfría antes de llenarse por completo, lo que da como resultado una pieza incompleta.
Arriba: Imágenes de cuando ocurre un plano corto. Abajo: forma de onda de serie de tiempo de presión cuando ocurre un defecto y cuando se produce un buen producto.
Después de evaluar los resultados de la prueba de tiro corto, los ingenieros concluyeron que los datos y las predicciones obtenidos de los sensores virtuales eran muy precisos.
Si bien la precisión es una prioridad principal tanto en el moldeo por inyección como en cualquier proceso de fabricación, la sostenibilidad se ha convertido en un objetivo igualmente importante.
Con una mayor conciencia ambiental impulsada por las preocupaciones sobre el calentamiento global y las iniciativas de neutralidad de carbono, las expectativas de alta eficiencia y procesos de ahorro de energía en el moldeo por inyección crecen cada año.
MAZIN confía en que la simulación puede ayudar al grupo a alcanzar los objetivos de sostenibilidad y cree que Twin Builder ya ha ayudado a reducir la huella de carbono de sus clientes.
“En el proceso de moldeo por inyección, los operadores suelen descartar productos hasta que la máquina de inyección lleva a un estado estable de producción de piezas viables”, dice Uchiyama. “Con la tecnología de gemelos digitales, se acorta el tiempo de espera para lograr un estado estable de la máquina y, por lo tanto, se reduce la huella de carbono para nuestros clientes”.
Éxito a gran escala
El interés por la startup japonesa ya ha crecido en todo el país. Global Brain, una firma de capital de riesgo con sede en Japón, anunció recientemente su apoyo a MAZIN como principal inversor.
A medida que MAZIN continúa expandiendo el negocio, Uchiyama dice que su equipo tiene la intención de mantener la simulación y la tecnología de gemelos digitales como componentes centrales de una operación exitosa.
“Desde una perspectiva de ingeniería, el uso de la simulación refuerza la solidez de nuestros productos”, dice Uchiyama. “Desde una perspectiva comercial, contribuye a nuestra estrategia de marca como una empresa emergente de tecnología”.
¿Que sigue? MAZIN planea usar la simulación para identificar defectos que no sean tiros cortos, incluyendo rebabas (exceso de moldeado), contracción (contracción del moldeado) y vetas plateadas (marcas plateadas en el moldeado causadas por bolsas de aire atrapadas durante un inicio rápido de la inyección).
Además, al equipo le gustaría crear sensores virtuales para condiciones fuera de la presión mediante el uso de mediciones combinadas de velocidad de flujo y temperatura.