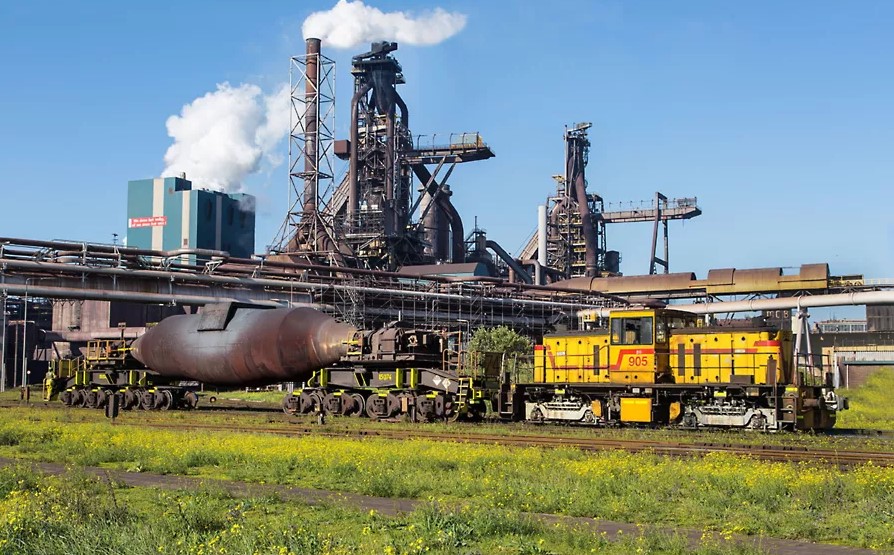
La simulación elimina fricciones en Tata Steel durante la producción de acero
La mayoría de los pasos de procesamiento en la fabricación de acero involucran altas temperaturas. Son estas temperaturas increíblemente altas las que pueden aumentar la demanda de energía y el mantenimiento de las siderúrgicas y plantear riesgos de seguridad inherentes para los trabajadores del acero. Combatir estas presiones competitivas requiere un ajuste cuidadoso de los procesos de fabricación y optimizaciones del diseño de la instalación que conduzcan a escenarios de producción más seguros y rentables.
Dejando a un lado la incertidumbre, Tata Steel Nederland (TSN), una de las principales siderúrgicas de Europa y parte del grupo Tata Steel, que es uno de los productores de acero más diversificados geográficamente del mundo, descartó un enfoque de producción de «prueba y error» para un uno más fiable basado en tecnologías digitales. Ansys es un socio importante en este proceso.
La acería IJmuiden de Tata Steel Nederland.
El Dr. Sido Sinnema, Líder del Grupo de Conocimiento del Grupo de Modelado Matemático e Ingeniería de Materiales (MEM), coordina un equipo de investigadores calificados y especialistas en materiales y modelado numérico para aplicaciones de alta temperatura. En este artículo, con el Dr. Bruno Luchini y el Dr. Paul van Beurden, nos explica el uso de la herramienta de simulación de Ansys en un entorno tan hostil.
“Parte de nuestras actividades de simulación implica la evaluación de varios escenarios para la optimización de procesos e instalaciones, así como el análisis de la causa raíz”, dice Luchini, investigador principal y líder del proyecto, R&D Ironmaking, Steelmaking, and Casting para Tata Steel Nederland. “La posibilidad de simular problemas multifísicos con productos Ansys nos permite evaluar mejor los mecanismos de falla de los distintos materiales/equipos presentes en la planta”.
“Ansys Mechanical se utiliza para desarrollar modelos termomecánicos sofisticados de método de elementos finitos (FEM) para investigar la relación entre las tasas de cambio de temperatura y las tensiones que se producen en el revestimiento refractario. El modelado de estas relaciones permite la optimización de los procedimientos de tratamiento térmico al tiempo que minimiza los riesgos de daños”, dice Van Beurden, investigador principal y líder del proyecto, R&D Ironmaking, Steelmaking, and Casting en Tata Steel Nederland.
Hora de controlar la temperatura
Un desafío inherente para Tata Steel es el mantenimiento de los hornos de recalentamiento de planchones. Durante paradas de mantenimiento más largas, los hornos deben enfriarse. Operando a 2,370 grados Fahrenheit, esta no es una tarea fácil, ya que simplemente apagarlos da como resultado un choque térmico que puede agrietar efectivamente el revestimiento del horno. Lo mismo es cierto para recalentar el horno. Cualquier cambio de temperatura debe ocurrir gradualmente para evitar daños costosos. Al mismo tiempo, enfriar o calentar el horno demasiado lentamente también puede resultar en la pérdida de una cantidad significativa de tiempo de producción.
La simulación de Ansys desempeñó un papel fundamental en la comprensión de la relación entre las tasas de temperatura del horno y el daño y la tensión del revestimiento refractario. Tata Steel Nederland mide las propiedades del material de sus refractarios en el laboratorio, luego mide las temperaturas del revestimiento del horno usando termopares. La integración de estos en un modelo termomecánico del horno permitió al fabricante de acero calcular las tensiones que se producen para comprender mejor lo que sucede durante los procedimientos regulares de calentamiento y enfriamiento.
En este escenario, Mechanical se usa para investigar qué sucede cuando las tasas de calentamiento o enfriamiento aumentan o disminuyen. Al hacerlo, los tiempos de enfriamiento y calentamiento podrían minimizarse. Como resultado, el equipo del MEM redujo el tiempo de inactividad del horno en 400 horas al año, aumentando la capacidad de producción de acero en más del 5 % y reduciendo significativamente el consumo de gas combustible y las emisiones de CO2.
En una parte anterior del proceso de producción, se produce y transporta arrabio líquido (o metal caliente), un producto intermedio en la producción de acero. Para mejorar el control del proceso y aumentar la confiabilidad de la producción del metal caliente líquido, es necesario poder predecir su temperatura en cualquier momento. Usando un modelo de proceso térmico FEM desarrollado en Mechanical y validado por mediciones de termopar, el campo de temperatura de las instalaciones de producción se puede simular y usar para derivar la temperatura del metal líquido. Sin embargo, la aplicación de dicho modelo FEM en la operación de procesos en tiempo real está limitada debido a los largos tiempos de cálculo.
En su lugar, se utilizó un modelo de orden reducido (ROM) basado en los resultados de la simulación del modelo FEM, como referencia, 1 segundo (ROM) frente a 2 horas (FEM), con menos de 0,1 °C en términos de diferencia de temperatura. Las ROM son un componente clave en las soluciones de gemelos digitales que pueden aprovechar simulaciones de alta fidelidad para optimizar las operaciones de procesos en tiempo real.
Un vagón portatorpedos transportado desde los altos hornos (visible al fondo) hasta la planta siderúrgica.
La simulación de Ansys se convierte en rutina
Tata Steel confía en varios productos de Ansys en total, incluidos Ansys SpaceClaim, Ansys Fluent, Ansys CFX, Ansys Maxwell y Mechanical. Durante mucho tiempo, el grupo también utilizó el lenguaje de diseño paramétrico de Ansys (APDL) para aplicaciones termomecánicas, y todavía mantiene varios modelos con características complejas que se ejecutan en APDL. Más recientemente, el equipo comenzó a usar Ansys Workbench y Ansys Twin Builder. Analizaron el uso de este producto en tres flujos de trabajo distintos para el análisis de causa raíz, la optimización de procesos y equipos, y el nuevo diseño de instalación.
Análisis de raíz de la causa
MEM utiliza rutinariamente software de simulación para flujos de trabajo de análisis de causa raíz para comprender mejor por qué una determinada instalación se comporta de una manera específica en la planta, o para evaluar la falla de un componente en particular. La simulación permite recopilar información sobre la geometría, las propiedades del material y las condiciones de contorno. Luego, los datos se utilizan para replicar virtualmente el escenario que enfrenta su equipo durante la operación que conduce a la falla. Una vez que se valida el modelo, las dimensiones del diseño, los materiales y las condiciones del proceso se pueden modificar para explicar el rendimiento actual de un diseño y, posteriormente, llegar a las mejoras de diseño adecuadas.
“Con este enfoque, pudimos examinar la derivación de las reglas de mantenimiento para el reemplazo de placas de enfriamiento en los altos hornos”, dice Sinnema. “Específicamente, las limitaciones de mantenimiento no permitieron reemplazar todas las placas de enfriamiento simultáneamente. El uso de un modelo FEM significaba que podíamos priorizar fácilmente el reemplazo de la placa de enfriamiento para una operación más segura y confiable”.
Optimización de Procesos y Equipos
Tata Steel Nederland también confía en los productos de Ansys para optimizar procesos y equipos. En este escenario, se crean modelos virtuales de equipos. Utilizando un enfoque paramétrico, el equipo identifica los parámetros clave y luego ajusta los parámetros del proceso necesarios para optimizar por completo tanto sus procesos como sus equipos clave. Es la versatilidad de estos modelos virtuales lo que permite al equipo explorar muchos escenarios mientras reduce la necesidad de una costosa experimentación física en la planta operativa.
Nuevo diseño de instalación
New Installation Design es el tercer flujo de trabajo en el que Tata Steel Nederland confía en los productos de Ansys. Para ello, se utiliza la simulación para comprobar los diseños de los proveedores eliminados numerosos escenarios antes de proponer mejoras. Este proceso fue fundamental en el diseño del nuevo horno de recalentamiento de TSN. El equipo usó la información recopilada para comprender mejor el impacto de las altas temperaturas varias veces antes de que el horno se pusiera en funcionamiento. Durante la fase de evaluación del proyecto, se utilizaron varios modelos FEM para ayudar en la selección de materiales, así como para la predicción precisa de la distribución de temperatura y las pérdidas de calor.
Los gemelos digitales aprovechan la simulación para mejorar las operaciones de procesos en tiempo real
Además de perder energía durante el proceso de fabricación, se pierde mucha energía durante el transporte de arrabio líquido en lo que se llama una cuchara de torpedo (es decir, un contenedor de transferencia especializado). Para negar la pérdida de energía durante el transporte, se utiliza un gemelo digital para modelar todo el proceso para determinar qué tan rápido, así como qué parámetro del proceso, el equipo puede ajustar para evaluar el mejor escenario de transporte.
Para el equipo del Dr. Sinnema, la tecnología de gemelos digitales se ha convertido en una evolución natural de su uso de herramientas de simulación de ingeniería. En el pasado, construían modelos separados para los equipos individuales de la planta. Por lo tanto, sus optimizaciones eran, por definición, subóptimas (optimizaciones locales). Con la tecnología del gemelo digital, el fabricante de acero podrá optimizar globalmente el proceso para conectar todos los distintos equipos de su cadena de producción y evaluar sus procesos con mayor detalle. Dichas pruebas pueden iluminar el impacto de los cambios en ciertas piezas del equipo en otras piezas, lo que lleva a una cadena de producción más limpia y ecológica.
“La combinación de un gemelo digital con otras innovaciones tecnológicas, como sensores inteligentes, nos ayudará a aprovechar la eficiencia energética de la planta y, a su vez, nos ayudará a lograr nuestros objetivos de descarbonización”, dice Luchini.
Tata Steel Nederland está pasando por una transformación sin precedentes en sus procesos de producción en la que el hidrógeno reemplazará al carbón. En 2030, TSN habrá implantado una planta de reducción directa (PRD) y un horno eléctrico reductor, ahorrando en torno a un 30-40% de emisiones de CO2.
“Planificar la puesta en marcha de dichos equipos y el desmantelamiento de otros no es tarea fácil. Es como cambiar neumáticos mientras el coche está en movimiento. Nuevamente, la tecnología de simulación es crucial en el diseño de los nuevos procesos”, dice Van Beurden.