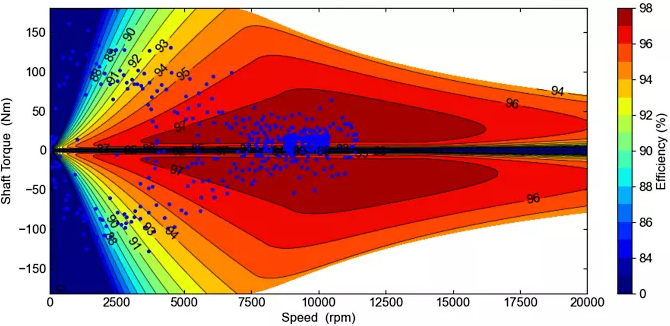
Diseño de bobinado en horquilla para máquinas eléctricas con Ansys
El bobinado con horquillas es una tecnología relativamente nueva en la que el sector del automóvil está cada vez más interesado debido a la creciente asequibilidad y eficacia de los procesos de fabricación.
En comparación con los devanados trenzados, las horquillas están formadas por conductores rectangulares. Esto supone un aumento significativo del factor de llenado de las ranuras en comparación con las soluciones tradicionales: Con los bobinados trenzados, los valores máximos se sitúan en torno a 0,45, mientras que la tecnología de horquillas llega hasta 0,8.
El principal inconveniente de esta solución es el complejo diseño de los patrones. Cuando se introducen trayectorias paralelas, hay que respetar varias reglas para obtener patrones de horquilla equilibrados electromagnéticamente.
Muchos fabricantes de equipos originales (OEM) de automoción se han pasado a esta tecnología en los últimos años. Esta solución de bobinado ofrece muchas ventajas para el diseño de máquinas eléctricas, que afectan al dimensionamiento electromagnético y a los sistemas de refrigeración.
Análisis electromagnético
Desde el punto de vista electromagnético, un mejor factor de llenado de las ranuras de cobre reduce el espacio dedicado a las ranuras y permite una densidad de par y potencia potencialmente mayores, junto con una reducción de la resistencia de CC. Suponiendo el mismo volumen de estator, una máquina con bobinado de horquilla puede estar menos saturada que su homóloga con bobinado trenzado, lo que se traduce en menores pérdidas de hierro. Esta es una ventaja clave, especialmente para los ciclos de accionamiento. Los motores de los vehículos eléctricos suelen tener un número reducido de espiras en serie. Esto significa que puede ser necesario un gran número de filamentos en mano, lo que provoca importantes pérdidas de CA. Un bobinado de horquilla con una combinación adecuada de capas y trayectos paralelos puede limitar estas pérdidas.
Ejemplo de diseño y comparación con una solución de bobinado trenzado
En la Figura 1 se muestra una comparación de diseño para un motor de aplicación de tracción. Las dos máquinas están diseñadas para la misma tensión, corriente y densidad de corriente de ranura; se han optimizado para obtener el mismo rendimiento de salida. El motor con devanado en horquilla permite un mayor diámetro interior del estator con respecto a la solución con devanado trenzado, con la ventaja de tener también una longitud de pila más corta y una mayor densidad de potencia. El menor volumen de hierro del estator también representa una ventaja a la hora de reducir las pérdidas de hierro.
Figura 1. Comparación de eficiencia y pérdidas entre el trenzado y la horquilla en un motor de tracción; las proporciones geométricas son las mismas en ambas imágenes.
Gracias a la menor resistencia de CC, la máquina de horquilla tiene claramente una mayor eficiencia en el punto base y una región de alta eficiencia significativamente mayor. Esto también se debe a las menores pérdidas de CA en la máquina de bobinado con horquilla. El bobinado de hilo requiere haces de hilos paralelos en la ranura para cumplir los requisitos de tensión y alcanzar un buen factor de llenado de la ranura de cobre. Estos haces, que representan las vueltas en serie efectivas, son especialmente propensos a sufrir grandes pérdidas de CA debido a las corrientes circulantes en los hilos paralelos. El diseño de bobinado de horquilla elegido, con ocho capas, tiene muchas menos pérdidas de CA, gracias también a una menor altura de la ranura.
Diseño de devanados en Ansys Motor-CAD y exportación a Ansys Maxwell
Ansys Motor-CAD calcula automáticamente el patrón de onda del devanado en horquilla, dividiendo el esquema en diferentes devanados elementales. Cada devanado elemental se construye para cumplir las normas de equilibrado de enlace de flujo que cubren todas las capas y todas las ranuras por polo y por fase, y representan una posible trayectoria paralela. Son posibles diferentes combinaciones de caminos paralelos poniendo en serie grupos de devanados elementales.
En la Figura 2, los devanados elementales se generan automáticamente, cubriendo todas las capas y ranuras por polo por fase. La matriz de bobinas se define para obtener el patrón de ondas (véase la figura 3). En este caso, son posibles ocho trayectorias paralelas, con la posibilidad de personalizar este número seleccionando los devanados elementales a poner en serie.
Figura 2. Esquema automático de bobinado de horquilla con 48 ranuras, 4 polos, 8 capas y 8 trayectorias paralelas.
Figura 3. Cada devanado elemental está diseñado para respetar las reglas de equilibrado del enlace de flujo y mostrar el patrón de onda típico de las conexiones finales.
Para un análisis más detallado de las corrientes circulantes en las trayectorias paralelas, el modelo Motor-CAD puede exportarse a Ansys Maxwell, donde puede realizarse la simulación con acoplamiento de circuitos externos.
Figura 4. Modelo Ansys Motor-CAD exportado a Ansys Maxwell.
Rendimiento del ciclo de accionamiento
Motor-CAD calcula fácilmente mapas de eficiencia y realiza análisis de ciclos de trabajo, proponiendo los ciclos de accionamiento más comunes como opciones predeterminadas.
En la Figura 5, se muestra el mapa de eficiencia de la máquina de horquilla, con los puntos de trabajo del ciclo de accionamiento US06 resaltados. La eficiencia media de esta máquina es del 94,23%.
Figura 5. Mapa de eficiencia de la bobinadora de horquilla y puntos de trabajo del ciclo de accionamiento US06.
El mismo análisis se realiza para el motor de bobinado trenzado y se muestra en la figura 6. Adoptando esta solución, el rendimiento medio desciende al 93,77%.
Figura 6. Mapa de eficiencia de la bobinadora de hilo y puntos de trabajo del ciclo de accionamiento US06.
Análisis térmico-electromagnético acoplado
El modelo térmico de Motor-CAD asigna correctamente las pérdidas de CC+CA a cada conductor individual. El perfil de temperatura resultante es discreto, como se muestra en la simulación de análisis de elementos finitos (FEA) de la Figura 7. El mismo concepto se adopta también para la red térmica. El mismo concepto se adopta también para la red térmica.
Figura 7. Modelo térmico para devanados en horquilla.
El modelo térmico es especialmente útil para evaluar el rendimiento de una máquina de velocidad variable en funcionamiento continuo. La figura 8 muestra la comparación de rendimiento entre la máquina de horquilla y la de trenzado, con el mismo sistema de refrigeración aplicado a ambas soluciones.
Figura 8. Comparación del rendimiento continuo entre las máquinas de horquilla y las de trenzado.
Evaluar las ventajas y desventajas de los devanados en horquilla y en espiral es un complejo reto multifísico que implica análisis electromagnéticos detallados y simulaciones térmicas. Las herramientas de Ansys le permiten comprender estas complejidades y tomar decisiones de diseño basadas en datos durante el proceso de desarrollo.
Ansys Motor-CAD calcula automáticamente patrones de onda factibles para los devanados en horquilla. Esta función ayuda a elegir el número adecuado de ranuras y combinaciones de capas en la fase inicial del diseño. Ansys Maxwell es capaz de realizar complejas simulaciones de elementos finitos y acopla los modelos FE al circuito externo para verificar la posible presencia de corrientes circulantes.
Por último, Motor-CAD acopla el análisis electromagnético al modelo térmico para calcular el rendimiento de la máquina teniendo en cuenta el sistema de refrigeración. Esto puede hacerse en la fase inicial del diseño y durante los procesos de optimización para evaluar el rendimiento térmico de diferentes soluciones de bobinado. Solicite su prueba gratuita de 30 días de Ansys Motor-CAD y tendrá acceso a todas las herramientas multifísicas necesarias para probar su próximo diseño de motor con bobinado en horquilla.