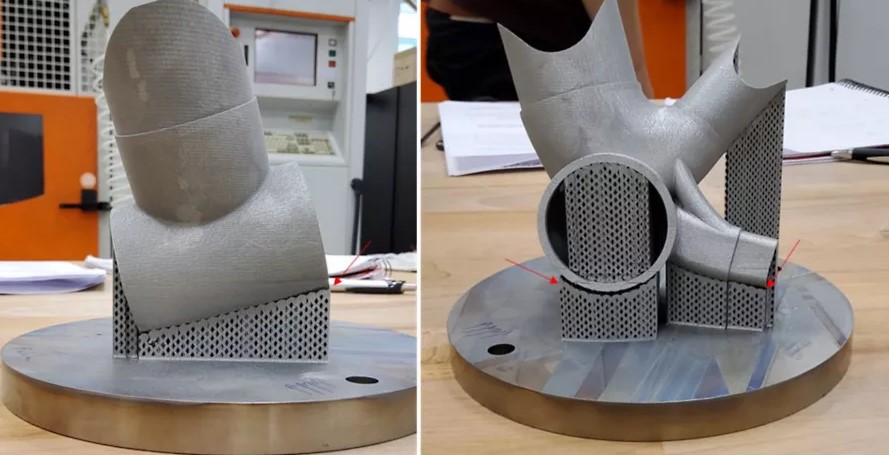
Ansys Additive Simulation une fuerzas con Aconity3D para imprimir un componente de bicicleta sin defectos
La fabricación aditiva, o impresión 3D, ha sido una palabra de moda durante más de una década. A medida que esta tecnología continúa evolucionando y expandiendo su valor en industrias como la aeroespacial, de defensa y de atención médica, sus ventajas únicas se vuelven más evidentes. Estos beneficios incluyen, entre otros, un alto grado de personalización del diseño, manufactura esbelta y aligeramiento. Son precisamente estas ventajas las que han llevado a un número cada vez mayor de industrias a adoptar la fabricación aditiva para complementar o incluso reemplazar las tecnologías de fabricación tradicionales. La industria de equipos deportivos personalizados de alta gama es un ejemplo reciente de esta tendencia, con el uso de la impresión 3D en la fabricación de bicicletas.
Siga leyendo para ver cómo se puede utilizar la impresión 3D para mejorar el diseño, la eficiencia en el uso de materiales y los procesos de fabricación de un componente de orejeta inferior de una bicicleta holandesa hecha a medida. También aprenderá cómo la colección de productos de simulación Ansys Additive juega un papel vital para ayudar a los ingenieros a lograr el éxito de impresión por primera vez como nunca antes.
Impresión íntegramente en 3D de una bicicleta en los Países Bajos
El campus de Brightlands Chemelot es uno de los cuatro campus de una comunidad de innovación abierta ubicada en la provincia de Limburg, Países Bajos. En Brightlands, los diseñadores, investigadores e ingenieros han colaborado para crear una bicicleta de carreras completamente impresa en 3D que cumple con las demandas de alto rendimiento de ser liviana y altamente personalizable, al mismo tiempo que mantiene una gran durabilidad y resistencia para condiciones de carretera impredecibles. Para lograr esto, han utilizado varios materiales de alto rendimiento y tecnologías de fabricación aditiva para crear un cuadro de bicicleta liviano, duradero y altamente personalizado.
La orejeta inferior, que conecta diferentes segmentos del cuadro de la bicicleta, es un componente fundamental en el diseño de la bicicleta. Para fabricar este componente, Brightlands trabajó con Aconity3D GmbH, un fabricante de máquinas líder en la industria y proveedor de soluciones de fabricación aditiva para la impresión 3D de metales basada en láser, ubicado en Aquisgrán, Alemania.
Figura 1. Bicicleta de carreras impresa en 3D de Brightlands y orejeta inferior. Imágenes cortesía de Brightlands Chemelot Campus.
Impresión 3D de una orejeta inferior de titanio en Aconity3D
Para garantizar que la orejeta inferior de la bicicleta diseñada a medida sea lo suficientemente fuerte como para soportar condiciones adversas sin dejar de ser liviana, se eligió Ti-6Al-4V como material de impresión. Este material es conocido por su fuerza específica superior y se usa ampliamente en aplicaciones aeroespaciales y médicas.
Durante el proceso de impresión, la orejeta inferior de la bicicleta se orientó como se muestra en la Figura 2, y se usaron una serie de estructuras de soporte generadas donde fue necesario, según la experiencia de impresión. Para realizar el trabajo de impresión, se utilizó un sistema de fusión de lecho de polvo láser (LPBF) AconityMIDI+ en Aconity3D GmbH. Si bien el componente de la bicicleta se imprimió relativamente bien, se produjo un problema inesperado.
Figura 2. Sistema Aconity MIDI+ LPBF y configuración de construcción inicial para la impresión de orejetas inferiores de bicicletas. Imágenes cortesía de Aconity GmbH.
Abordar los desafíos de la delaminación durante el proceso LPBF
Las estructuras de soporte comúnmente utilizadas en construcciones LPBF son para restringir posibles deformaciones de piezas no deseadas. En muchos casos, los soportes pueden ser demasiado débiles para sostener una unión firme a la geometría de la pieza construida debido a la alta tensión heredada del proceso de construcción. Como se ve en la Figura 3, debido a los efectos de acumulación de alta tensión, se produjeron deslaminaciones críticas en las interfaces entre la parte de orejeta inferior construida y las estructuras de soporte. Tal deslaminación típicamente ocurre cuando la tensión en ese lugar excede el alargamiento que un material puede soportar. Como resultado, las estructuras de soporte no pudieron restringir de manera efectiva las deformaciones de la pieza construida, lo que podría generar problemas con las tolerancias geométricas.
Figura 3. Defectos de delaminación observados en regiones críticas en la interfaz entre la parte inferior de la orejeta y las estructuras de soporte. Imágenes cortesía de Aconity GmbH.
La detección aditiva de alta tensión de Ansys ayuda a identificar regiones críticas durante la construcción de LPBF
Para resolver este defecto de delaminación de la estructura de soporte, Ansys y Aconity3D unieron fuerzas al integrar simulaciones de procesos de fabricación aditiva en el flujo de trabajo de fabricación. Se utilizaron simulaciones Ansys Additive LPBF para identificar rápidamente las áreas críticas y evaluar la orientación de la construcción y las estrategias de apoyo. La herramienta de resultados de alta tensión de simulación LPBF destaca las regiones críticas de tensión, lo que permite a los ingenieros identificar regiones de la pieza que pueden ser propensas a la formación de grietas durante o después de la construcción. Con base en los resultados de la simulación, se implementó una estrategia optimizada para la impresión de validación física en un sistema Aconity MIDI+ LPBF de última generación.
En primer lugar, se utilizó un modelo estructural estático de tensión inherente para simular la configuración de la construcción con las orientaciones de construcción exactas y las estructuras de soporte de la construcción defectuosa. La función de alta tensión se agregó a la sección de resultados de la simulación para detectar las regiones críticas con acumulación de alta tensión durante el proceso de impresión.
Al revisar los resultados de la simulación, las regiones de alta tensión identificadas coincidieron estrechamente con las ubicaciones donde ocurrieron las delaminaciones durante la construcción real. Estas áreas probablemente servirían como sitios de iniciación para la deslaminación, que luego se propagaría rápidamente a través de la interfaz adyacente entre la parte inferior de la lengüeta y las estructuras de soporte.
Al realizar una evaluación de simulación de la primera construcción de impresión, se demostró que la función de detección de alta tensión de la simulación de Ansys Additive ofrece con éxito un mapeo de alta fidelidad a las áreas críticas que se observaron y verificaron en la construcción física.
Figura 4. La simulación de Ansys Additive LPBF captura las mismas regiones críticas donde se produjeron deslaminaciones en la construcción física utilizando la función de detección de alta tensión.
El siguiente paso consiste en mejorar la orientación de la construcción y las estructuras de soporte para evitar defectos de delaminación. Para lograr esto, los ingenieros de Aconity3D dieron un salto de certeza al colaborar con la simulación de Ansys Additive antes de proceder con la siguiente construcción física.
Según los resultados de la construcción anterior, AconityMIDI+ produjo una gran pieza de componente, a pesar de que la gran tensión se producía en la interfaz entre la pieza y los soportes, lo que provocaba deslaminaciones. Para imprimirlo aún mejor, los ingenieros de Aconity3D revisaron las orientaciones de construcción y fortalecieron las estructuras de soporte en áreas cruciales. En lugar de imprimir directamente la siguiente compilación, se asociaron con Ansys para realizar una simulación preliminar con la detección de alta tensión habilitada para la configuración de la nueva compilación. Los resultados de la simulación indicaron una reducción significativa en las regiones de alta tensión a lo largo de la interfaz entre la parte de orejeta inferior recién orientada y las estructuras de soporte, en comparación con la configuración de construcción anterior.
Al incorporar simulaciones de procesos en el flujo de trabajo de fabricación de Aconity3D, los ingenieros de procesos pueden evaluar y validar fácilmente diferentes estrategias de orientación y soporte primero en la simulación, antes de enviar los archivos de construcción a la planta de máquinas. Por lo tanto, la integración exitosa de la simulación aumenta la eficiencia y reduce el tiempo y el costo al reducir la cantidad de impresiones de prueba.
Figura 5. Nueva configuración de construcción de orejetas inferiores con orientaciones de construcción revisadas y estructuras de soporte mejoradas.
Lograr piezas sin defectos y objetivos de impresión correcta a la primera
Al combinar las simulaciones de Ansys Additive en el flujo de trabajo, los ingenieros de Aconity3D pudieron abordar la impresión de la parte de la lengüeta inferior reorientada con mayor confianza. Reforzaron con éxito las estructuras de soporte en regiones críticas, lo que dio como resultado un producto final sin defectos que cumplió con sus expectativas cuando salió de la cámara del sistema AconityMIDI+.
Figura 6. Orejeta inferior sin defectos de delaminación fabricada utilizando las estructuras de soporte y orientación de construcción nueva. Imagen cortesía de Aconity GmbH.
El éxito de la colaboración entre Ansys y Aconity3D ha dado como resultado la impresión perfecta de este componente de lengüeta inferior. Una vez que el componente se ensambló en la bicicleta de carreras en el campus de Brightlands Chemelot, Menno Smeelen, el nuevo gerente de desarrollo comercial, estaba encantado de probarlo. La bicicleta se desempeñó excepcionalmente bien, brindando el alto rendimiento, la durabilidad y la resistencia necesarios para terrenos desafiantes.
Figura 7. Menno Smeelen de Brightlands monta la bicicleta de carreras ensamblada con una orejeta inferior impresa en 3D. Imagen cortesía de Brightlands Chemelot Campus.